Inspection Machines
The success and profitability of your operation depend on the quality of your finished goods. Product failures and inconsistencies at best will cost you money, and at worse cost you business. Inspection machines provide a layer of quality assurance through the examination of products and material components to ensure they meet all specifications. Hybrid Engineering is highly experienced in the development of reliable inspection machines.
When considering an investment in dependable inspection machines, consider what you get for your money. Hybrid Engineering designs inspection machines for constant reliability at a low cost to maintain. To deliver the most benefit, your inspection machines should be tailor engineered to suit your products and processes. Hybrid Engineering will begin developing your inspection machine with a careful analysis of your application. You can count on your system to achieve the level of inspection precision and accuracy you require for complete confidence.
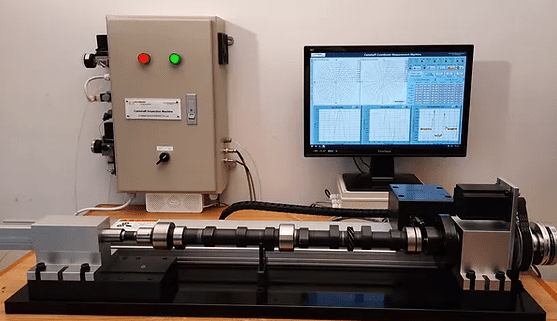
Camshaft Inspection machine
Parameters Measures: Cam lift curve | Cam phase angle | Bearing shaft runout | Keyway angular position | Lift velocity curve | Lift acceleration curve
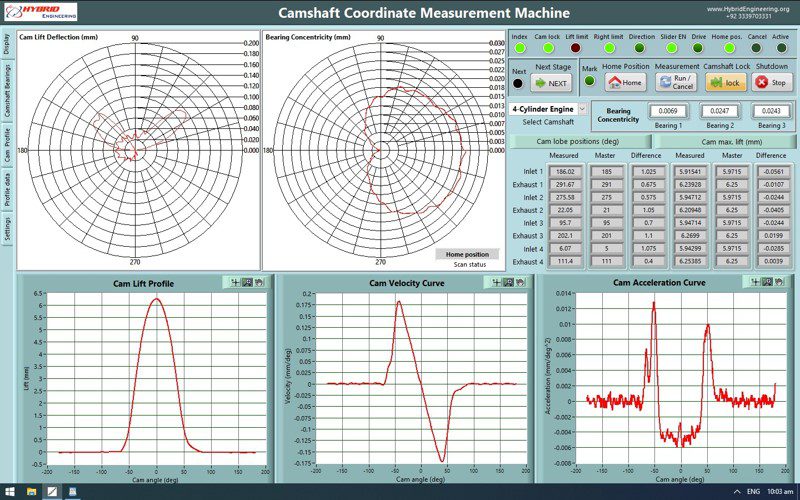
Repeatability within 1 micron, Sensor resolution 0.3 micron, Phase angle resolution 0.0125 degree
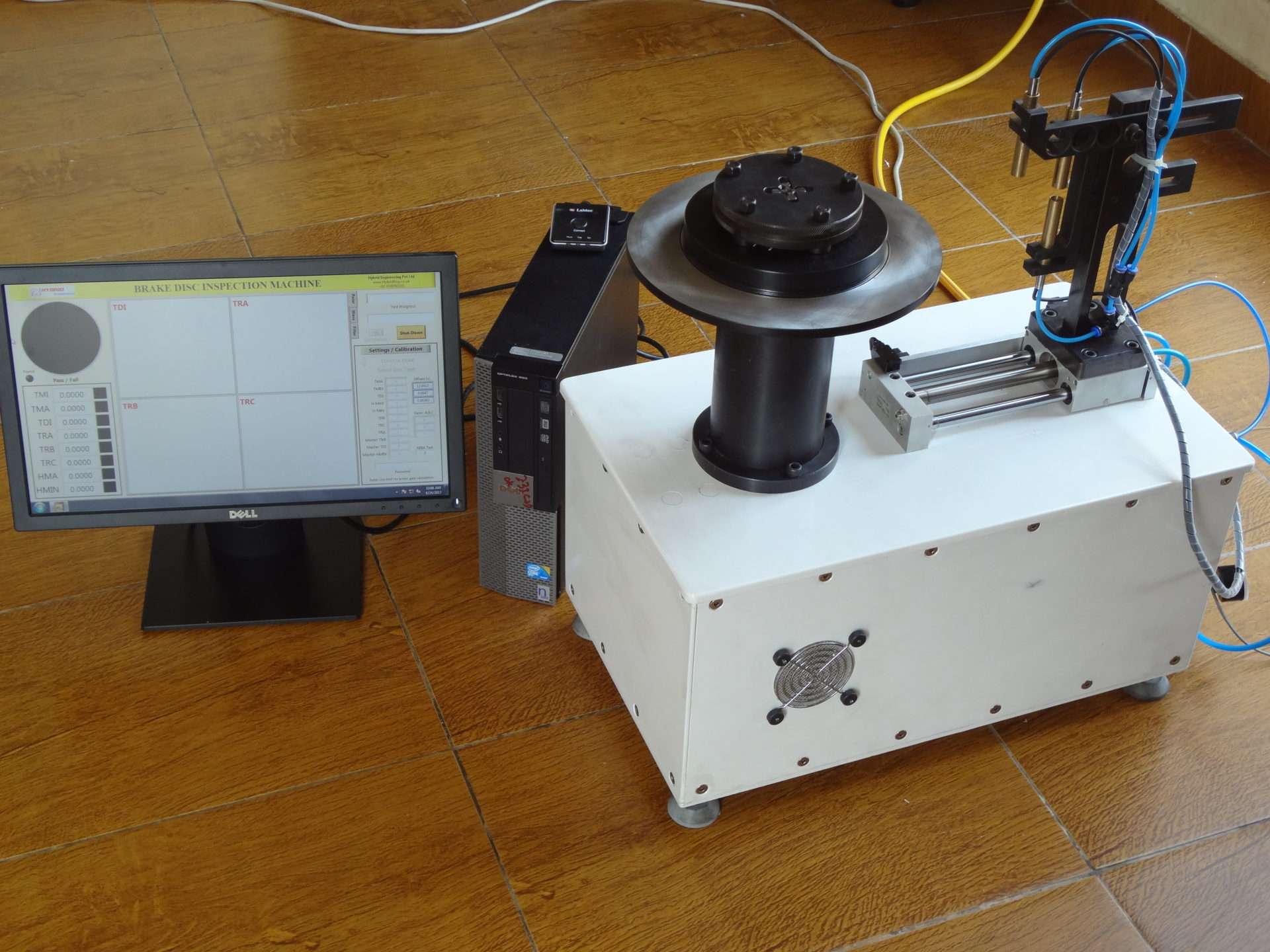
Automated Brake Disc Inspection Machine
Customized Brake Disc Inspection Machine developed for Auto OEM at a fraction cost of Imported machines with higher accuracy.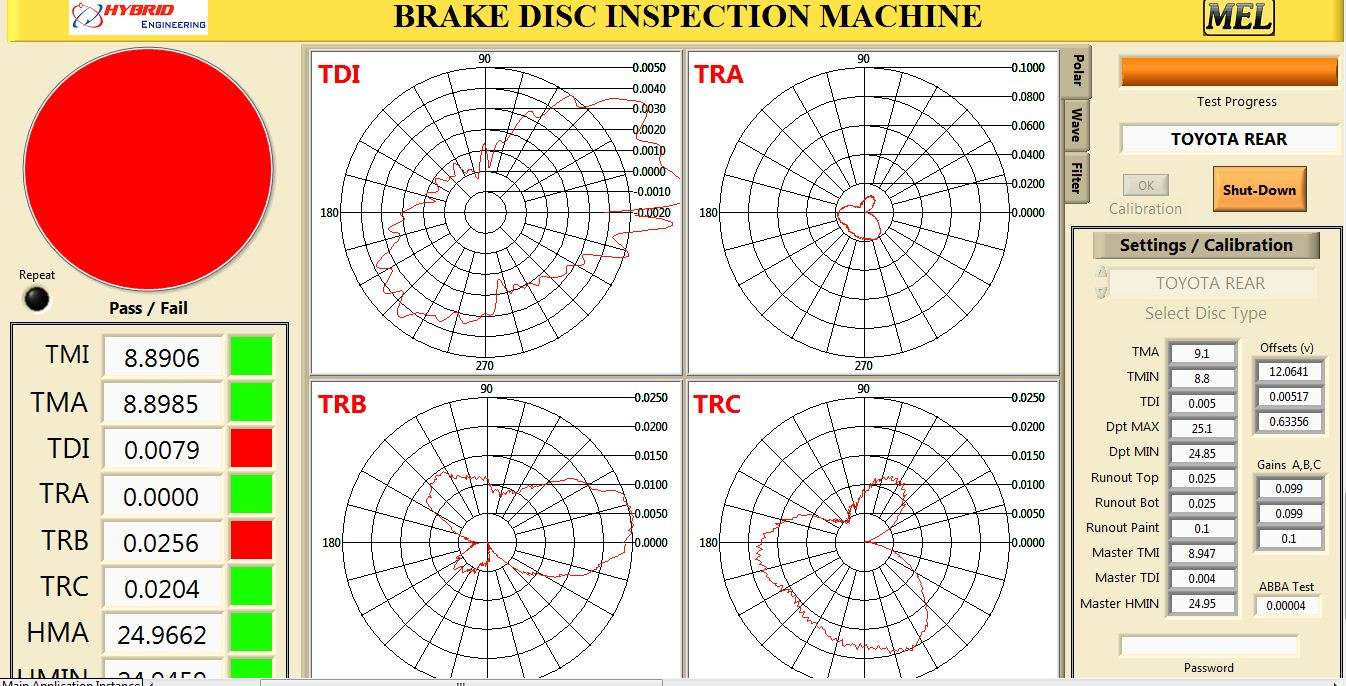
This inspection machines measures 15 different parameters. The accuracy of crucial parameters is more than a micron. The machines comes with an advanced user friendly software.
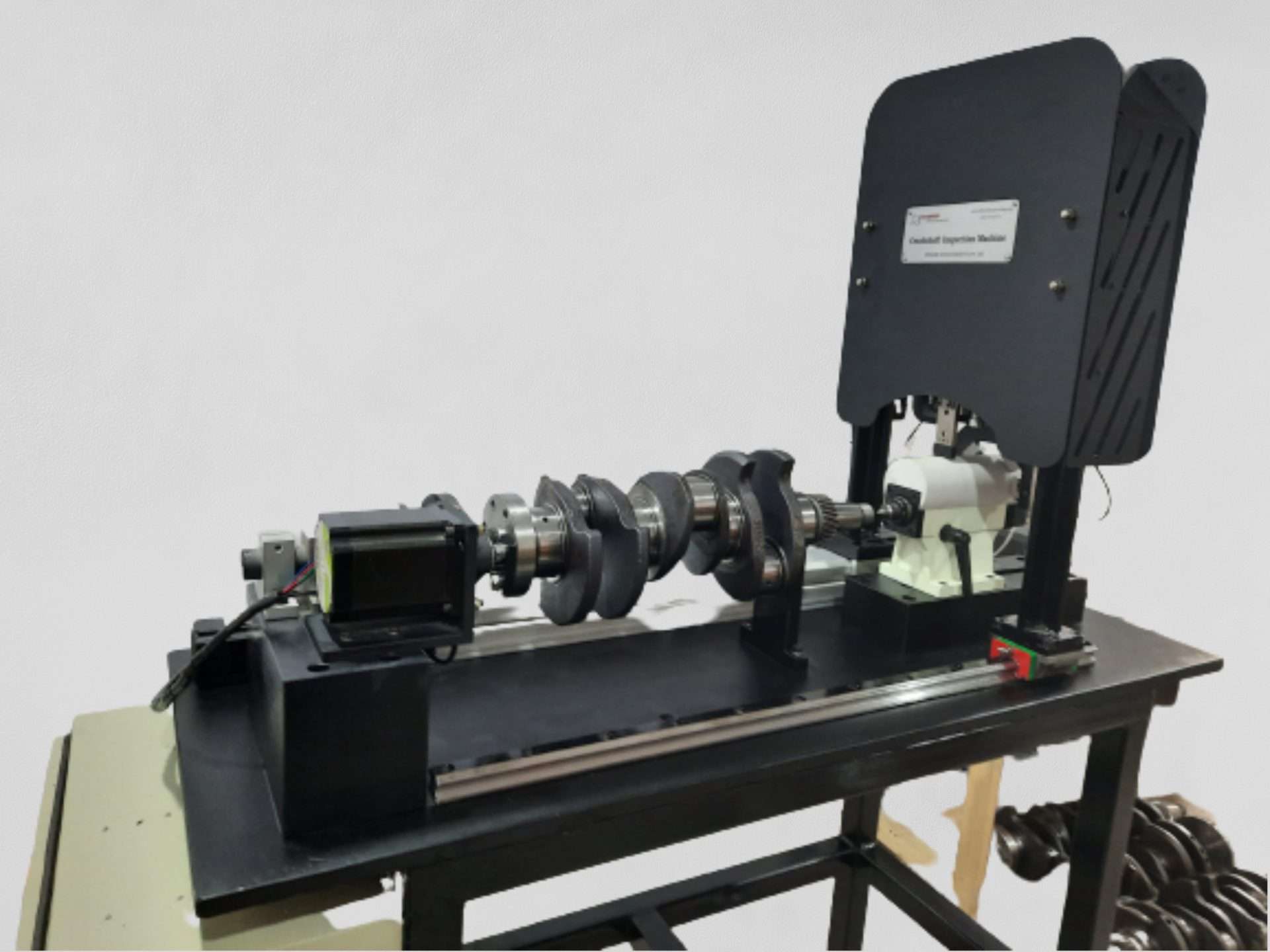
Crankshaft Inspection Machine
Parameters Measures: Diameter profiling of journal and crank pin | Tapper measurement of journal and crank pin | Runout of journal.

Repeatability within 1 micron. Sensor resolution 0.3 micron. Phase angle resolution 0.125 degree
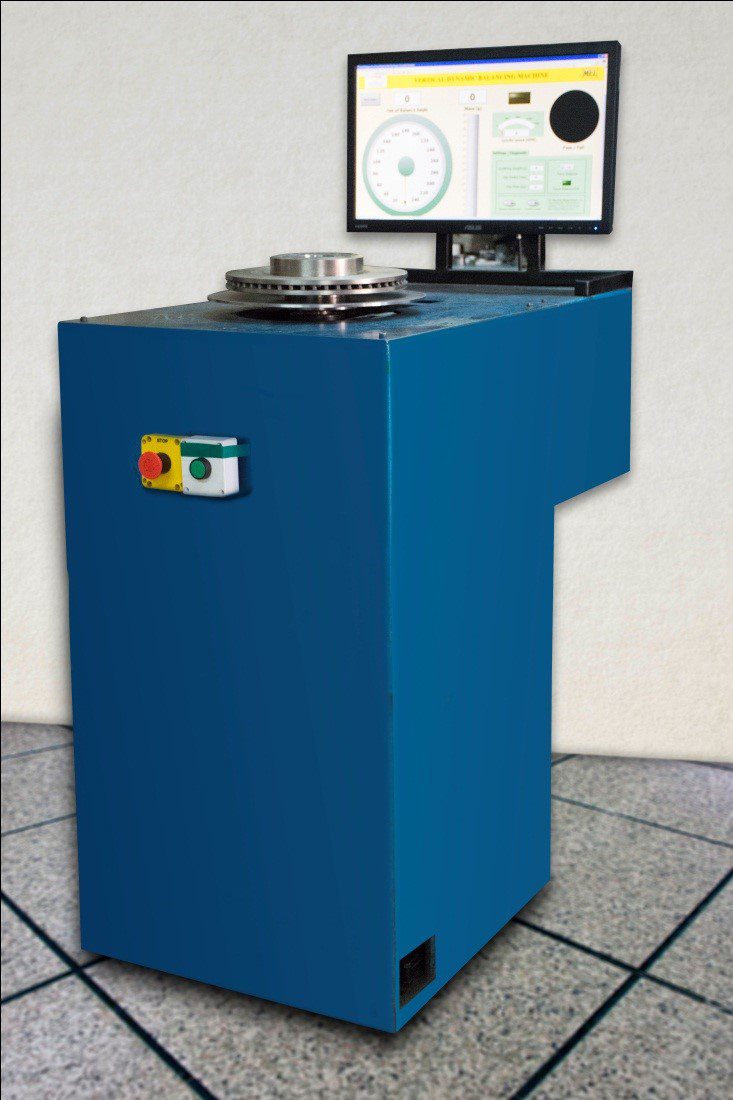
Vertical Balancing Machine
Advanced data acquisition system, sensor technology and precision drive mechanism are used in the vibration analysis to assist in the balancing process.
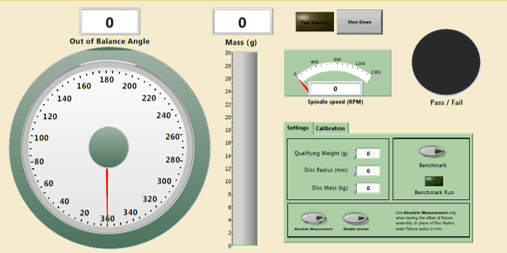
The vibration level measured at the rotating speed frequency is used as an indicator of the amount of unbalance. The location is determined by measuring the phase. Phase, (the relative motion of one part of a machine to another) is measured by means of pickup sensor and counter chip, triggered by a photocell.
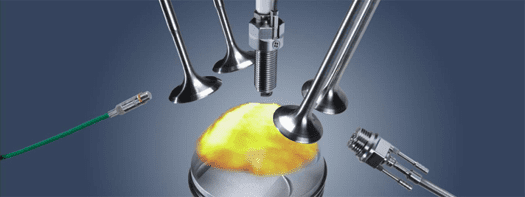
Combustion Analyzer
One of its kind developed for tractor OEM.

Synchronized measurement of inlet manifold, exhaust manifold and combustion chamber pressure measurement for all 4 units for combustion tuning to improve engine performance and emissions.
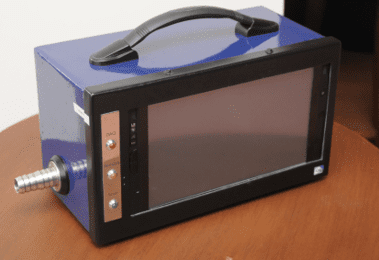
Engine Blowby Measurement System
One of the most challenging parameters to measure accurately in engine testing is engine blow-by. The blow-by flow rate of engines is very low and thus is difficult to measure through conventional means. Special techniques are used to measure such limited flow rates.
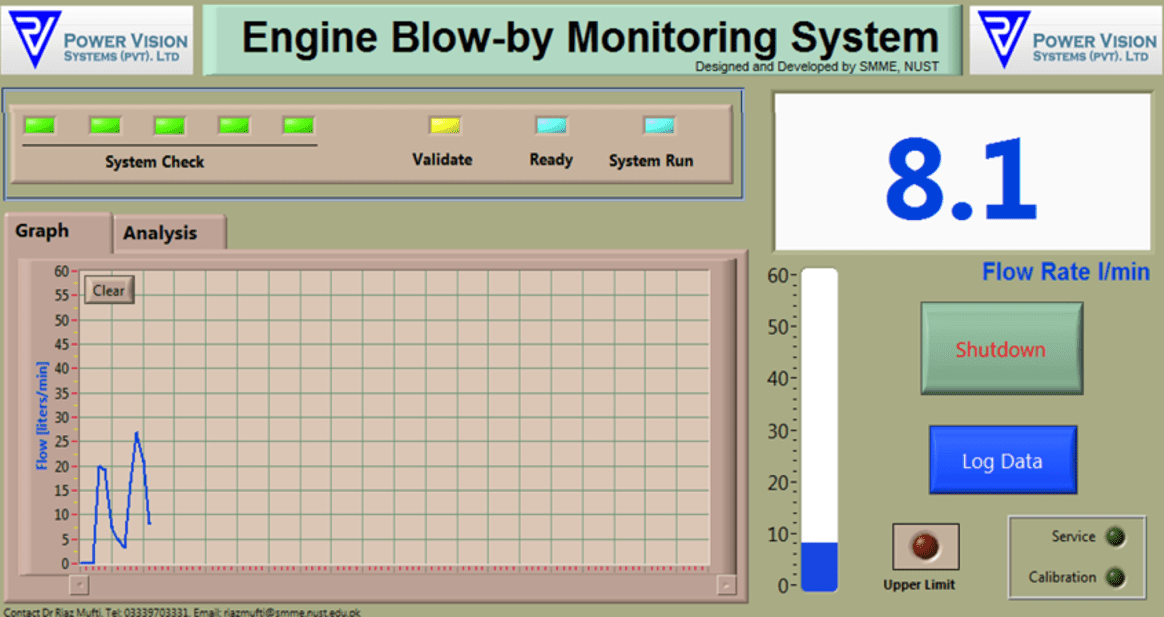
Engineers designed and developed Engine Blow-by Monitoring System with the flexibility to tailor the user interface according to the customers requirements. This system utilizes the advanced embedded system coupled with sensitive flow system. The in-built advanced DAQ system logs the data for analysis, validates and performs signal conditioning.
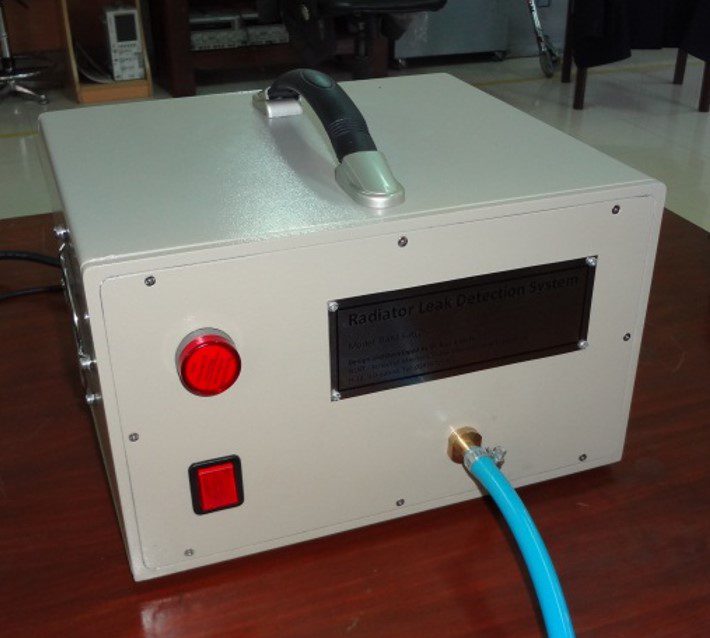
Leak Detection System for Radiators
One of the main advantage of using our system for leak detection is that the product is shipped in mint condition with no scale marks on the product.
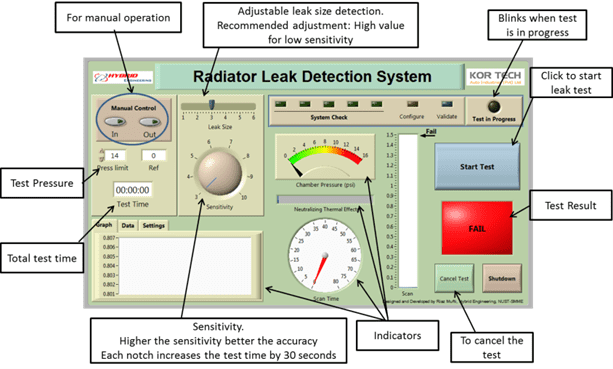
The leak is detected through pressure decay, pressure differential and air mass flow rate. The system can be connected to a PC via usb port. User friendly software gives the user complete control. Leak size and sensitivity can be adjusted with a click of a button.
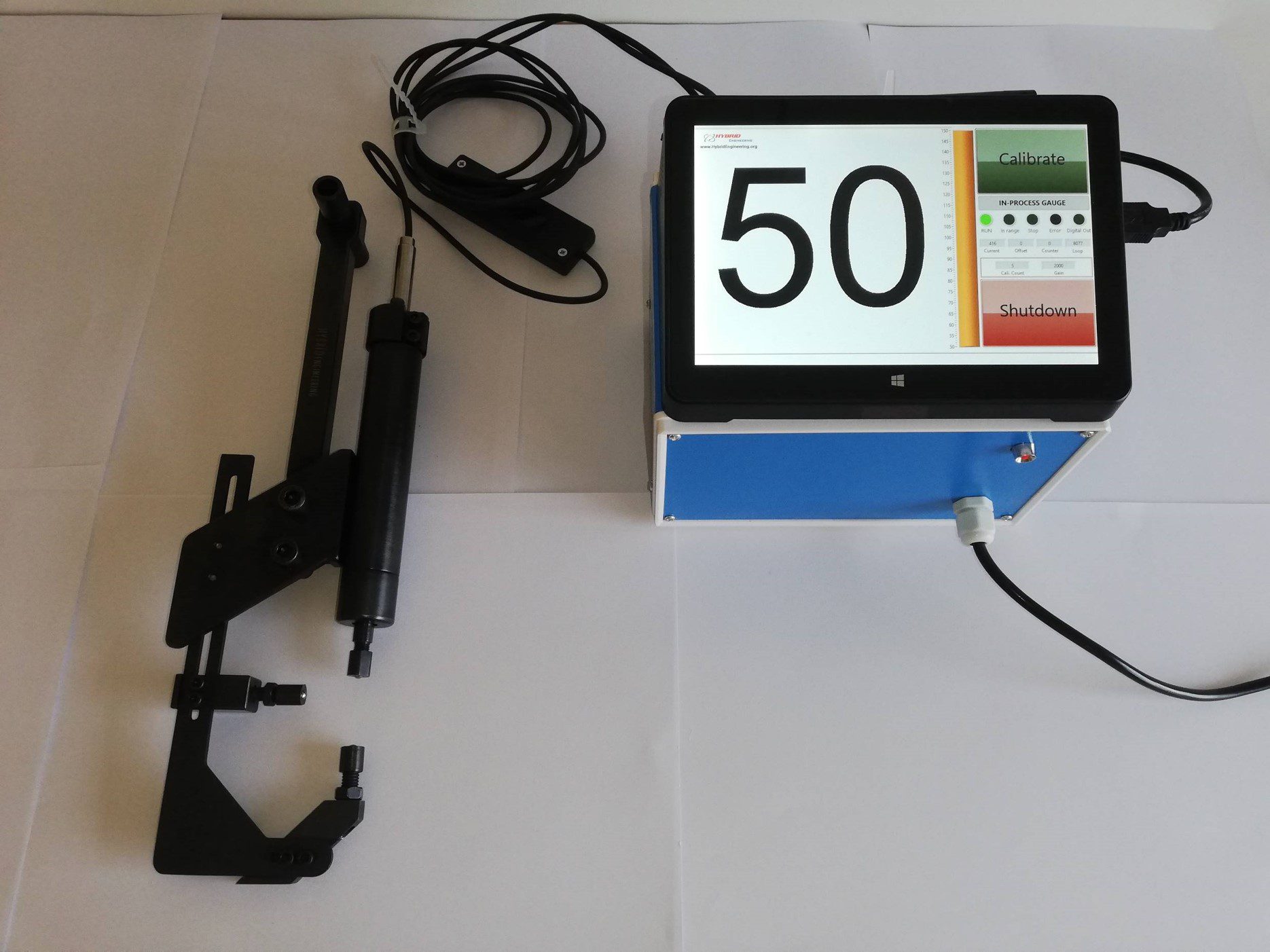
Inprocess Grinding Gauge
The in-process grinding gauge measures shaft diameter during the part grinding process. The gauge automatically monitors the part diameter while grinding in order to control finished part size upto the required diameter.
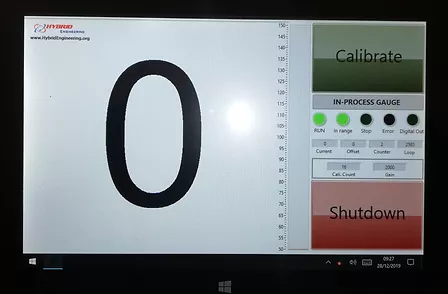
The gauge, together with the associated data-acquisition system exchanges information and signals with the grinding machine in order to maximize performance and achieve the desired results.
Inspection Machines
More and more manufacturers are adopting automated quality control systems in order to detect issues before it is too late or to reduce quality control costs. Our automated quality inspection machines enhance overall product quality, increase throughput, mitigate obsolete and cumbersome manual inspections, and improve competitiveness.
Need Customized Inspection System?
global relationships
Our Customers
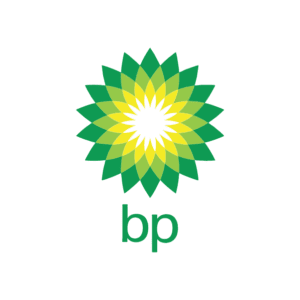
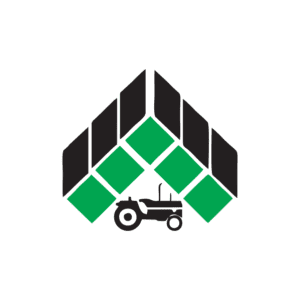
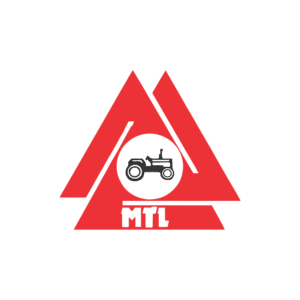
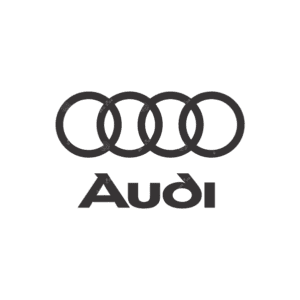
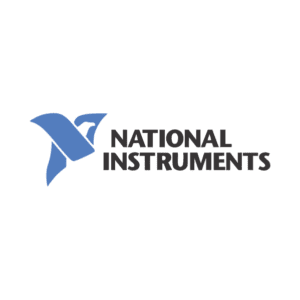
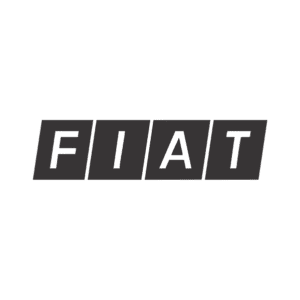